Safety Best Practices
Stefano Braganti
Real-Time Workforce Visibility Ends Labor Drift & Rework
Labor drift, rework and schedule slips thrive when you can't see head-count live. Learn how smart turnstiles & dashboards give GCs real-time visibility.
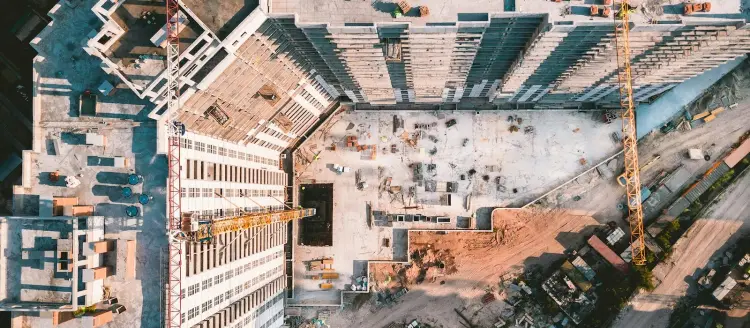
The construction industry is confronting a harsh reality: falls remain the leading cause of fatalities among workers. According to the Occupational Safety and Health Administration (OSHA) and the Bureau of Labor Statistics data, of the 1,008 total construction-related deaths reported in 2020, 351 were attributed to fatal falls to a lower level. The stark truth is that these tragedies were entirely preventable.
To combat this ongoing issue, OSHA has joined forces with the National Institute for Occupational Safety and Health and the National Occupational Research Agenda (NORA) - Construction Sector. Together, since 2012, they have led the Fall Prevention Campaign to raise awareness among both workers and employers about the common hazards leading to falls in construction. These include, but are not limited to, falls from ladders, scaffolds, and roofs.
Many of these accidents occur because of the improper use of fall protection equipment, lack of its usage, or failure by employers to provide it. These are oversights that should not occur.
To tackle this issue head-on and reduce fall-related fatalities, OSHA advocates a comprehensive three-part strategy: Plan, Provide, and Train.
Safety planning is a critical element of any job involving work from heights. Employers should start by mapping out how the job will be done, the tasks involved, and the safety equipment required to complete each task safely.
Cost estimation should include the safety equipment, and all necessary tools and gear should be readily available at the construction site. For instance, in a roofing job, anticipate potential fall hazards like holes, skylights, and leading edges, and plan to use suitable fall protection such as personal fall arrest systems (PFAS).
Safety at six feet or more above lower levels is paramount. To prevent injuries or fatalities from falls, employers must provide adequate fall protection and appropriate equipment for the job, which includes ladders, scaffolds, and safety gear.
Choose the correct ladder or scaffold for safe job completion. For roof work, if workers use personal fall arrest systems (PFAS), each worker who will be anchoring must be provided with a harness. Ensure that the PFAS is a good fit for each user and routinely inspect them for safety.
Proper training is the linchpin of a safe work environment. Every worker should understand how to set up and use the equipment safely. Employers should train workers to recognize hazards and use equipment like ladders, scaffolds, and fall protection systems safely.
Workers should be trained in ladder safety, including maintaining three points of contact, placing the ladder on level footing, securing the ladder, not overreaching, and not moving the ladder while on it. Scaffold safety involves fully planking scaffolds, installing all guardrails, ensuring stable footing, leveling, and having a competent person inspect the scaffold before use.
For roof work, workers should know how to avoid fall hazards, ensure their harness fits properly, always stay connected/tie off, ensure all anchor points are safe, and protect all holes, openings, and skylights.
Falls in the construction industry, while tragically common, are entirely preventable. Employers hold the key to significantly reducing these incidents by prioritizing the planning of safe work procedures, providing appropriate safety equipment, and implementing comprehensive training programs. The three-step strategy of planning, providing, and training forms the bedrock of any effective fall prevention approach. By diligently adhering to these strategies, we can create a safer construction environment where the preservation of life is paramount. A commitment to these principles ensures that every construction worker has the right and the means to return home safely at the end of the day. Our collective efforts can change the narrative, making construction fatalities a thing of the past.
Risk Manager with 10+ years of experience in the construction industry. Passionate supporter of the NFL's New York Giants.
Safety Best Practices
Stefano Braganti
Labor drift, rework and schedule slips thrive when you can't see head-count live. Learn how smart turnstiles & dashboards give GCs real-time visibility.
Safety Best Practices
Stefano Braganti
Stop-Work Orders crush margins. Digital safety dashboards catch risks early, prevent claims, and protect your 3% fee.
Safety Best Practices
Stefano Braganti
NYC DOB formalizes digital record-keeping: what the bulletin says, why it matters, and how SafetyClerk helped make it happen.
together
SafetyClerk is the construction management platform that makes safety compliance, and risk management of your job site simple and visible in one click.
Stay on
the loop!
ConstructionClerk - 2025 - All rights reserved
ConstructionClerk - 2025 - All rights reserved