Safety Best Practices
Stefano Braganti
Real-Time Workforce Visibility Ends Labor Drift & Rework
Labor drift, rework and schedule slips thrive when you can't see head-count live. Learn how smart turnstiles & dashboards give GCs real-time visibility.
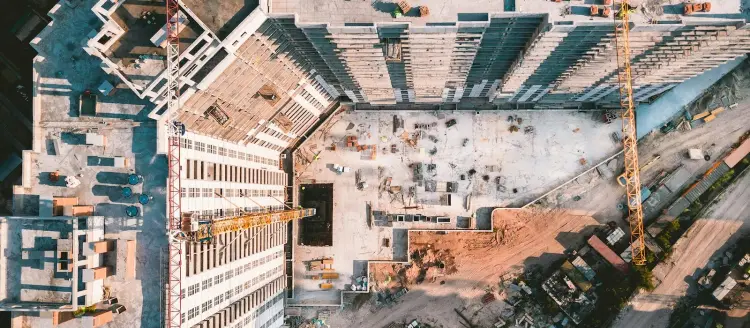
Construction helmets, also known as hard hats, are essential personal protective equipment (PPE) designed to protect workers from head injuries. This guide will help you understand the importance of construction helmets, the different types available, and how to choose the right one for your needs.
Construction helmets are crucial for protecting workers from various hazards, including falling objects, electrical shocks, and impacts. They are designed to absorb and distribute the force of impacts, reducing the risk of serious head injuries. Wearing a helmet is not only a safety requirement but also a best practice for maintaining a safe work environment.
There are several types of construction helmets available, each designed for specific hazards and conditions:
Type I Helmets: These helmets are designed to protect against impacts to the top of the head. They are suitable for general construction work where the primary hazard is falling objects.
Type II Helmets: These helmets provide protection against impacts to both the top and sides of the head. They are ideal for environments where lateral impacts are a concern.
Class G (General) Helmets: These helmets are designed to reduce the risk of electrical shocks. They are suitable for environments where workers may be exposed to low-voltage electrical hazards.
Class E (Electrical) Helmets: These helmets provide the highest level of electrical protection and are suitable for environments with high-voltage electrical hazards.
Class C (Conductive) Helmets: These helmets are not designed to provide electrical protection and are suitable for environments where electrical hazards are not a concern.
When selecting a construction helmet, consider the following factors:
Hazard Assessment: Identify the specific hazards present in your work environment to determine the type of helmet needed.
Comfort and Fit: Ensure the helmet fits properly and is comfortable to wear for extended periods. Adjustable suspension systems can help achieve a secure fit.
Durability: Choose a helmet made from high-quality materials that can withstand the rigors of construction work.
Compliance with Standards: Ensure the helmet meets relevant safety standards, such as those set by the American National Standards Institute (ANSI) or the Occupational Safety and Health Administration (OSHA).
Proper maintenance and care are essential for ensuring the effectiveness of construction helmets:
Regular Inspection: Inspect the helmet regularly for signs of damage, such as cracks, dents, or wear. Replace any damaged helmets immediately.
Cleaning: Clean the helmet regularly with mild soap and water to remove dirt and debris. Avoid using harsh chemicals that could damage the helmet.
Storage: Store the helmet in a cool, dry place away from direct sunlight and extreme temperatures.
Construction helmets are a vital component of workplace safety, providing essential protection against head injuries. By understanding the different types of helmets, choosing the right one for your needs, and maintaining it properly, you can ensure a safer work environment for yourself and your team. Prioritizing safety not only protects workers but also enhances productivity and morale on the job site.
Safety Best Practices
Stefano Braganti
Labor drift, rework and schedule slips thrive when you can't see head-count live. Learn how smart turnstiles & dashboards give GCs real-time visibility.
Safety Best Practices
Stefano Braganti
Stop-Work Orders crush margins. Digital safety dashboards catch risks early, prevent claims, and protect your 3% fee.
Safety Best Practices
Stefano Braganti
NYC DOB formalizes digital record-keeping: what the bulletin says, why it matters, and how SafetyClerk helped make it happen.
together
SafetyClerk is the construction management platform that makes safety compliance, and risk management of your job site simple and visible in one click.
Stay on
the loop!
ConstructionClerk - 2025 - All rights reserved
ConstructionClerk - 2025 - All rights reserved