Safety Best Practices
Stefano Braganti
Real-Time Workforce Visibility Ends Labor Drift & Rework
Labor drift, rework and schedule slips thrive when you can't see head-count live. Learn how smart turnstiles & dashboards give GCs real-time visibility.
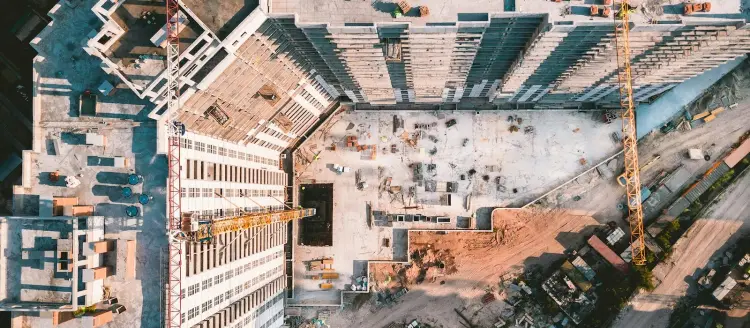
Construction sites are inherently hazardous environments, where workers face numerous risks on a daily basis. To mitigate these risks and ensure the safety of everyone involved, the implementation of comprehensive safety protocols is essential. One such protocol that has proven to be highly effective is the Pre-Task Plan, also known as Pre Shift Plan. In this blog post, we will explore the significance of Pre-Task Plans in construction, their role in accident prevention, and best practices for their implementation.
A Pre-Task Plan is a proactive approach to identify and mitigate potential hazards before commencing any construction activity. It involves a systematic analysis of the job, breaking it down into specific tasks, assessing associated risks, and implementing control measures to prevent accidents. For example, let's consider a painter painting walls:
This example showcases one of many Task-Risk-Control combinations that could be covered during a Pre-Task Plan. By outlining and assigning every task to the crews, the foreman reminds workers of the risks and the countermeasures associated with each task. This plan serves as a roadmap for workers, outlining the sequence of activities, potential hazards, and appropriate safety measures.
Statistics show that a significant number of construction accidents (more than 75%!) occur when Pre-Task Plans are not in place. By neglecting this critical step, workers may unknowingly expose themselves and others to avoidable hazards. Pre-Task Plans provide the following benefits:
a. Accident Prevention: Pre-Task Plans enable construction teams to anticipate and address potential hazards, minimizing the likelihood of accidents and injuries. They promote a proactive safety culture by identifying and controlling risks before work begins.
b. Efficient Resource Allocation: With a well-developed Pre-Task Plan, construction teams can allocate resources effectively, ensuring that the right equipment, materials, and personnel are available at the right time. This leads to enhanced productivity and streamlined operations.
c. Legal Protection: As a company, providing the best safety measures and training for workers on-site is crucial. However, workers also have a duty to adhere to safety recommendations. Developing, implementing, and documenting a robust Pre-Task Plans policy creates backup documentation in case of accidents or insurance claims. For example, if a worker falls from a ladder while painting a ceiling due to improper ladder use, your position in a subsequent insurance claim could be stronger if you can show that your foreman held Pre-Task Plans every day for the last year, explaining the task of painting the wall, the risk of falling from the ladder, and how to properly use a ladder as a control measure.
In some jurisdictions, such as New York City, where Pre-Task Plans were made mandatory in 2018 (as outlined in the NYC Department of Buildings' Industry Notice LL204), adherence to Pre-Task Planning is a legal requirement. Compliance not only avoids penalties but also demonstrates a commitment to worker safety.
The Job Hazard Analysis (JHA) is a systematic process used to identify and assess potential hazards associated with the overall job of a trade or construction manager. It serves as a comprehensive "cookbook," encompassing dozens, if not hundreds, of Task/Risk/Control combinations that cover the entire scope of work. Just like a cookbook provides a wide range of recipes, the JHA identifies hazards and control measures for each task.
On the other hand, the Pre-Task Plan (or Pre Shift) can be compared to daily receipts in cooking. It focuses on the specific tasks to be performed on a given day, which are derived from the larger JHA. While the JHA provides a holistic view of hazards and controls, the Pre-Task Plan zooms in on the smaller subset of tasks for the day. Think of it as the daily recipe list that ensures the necessary safety measures and controls are in place for the immediate activities.
Developing a Job Hazard Analysis (JHA) involves a systematic process to identify and assess potential hazards associated with a specific job or task. Here are the key steps to develop a JHA:
a. Break Down the Scope of Work: Start by making a list of all the tasks and sub-tasks that you will have to perform to complete the scope of work assigned to your company. This comprehensive breakdown will help ensure that no potential hazards are overlooked.
b. Identify Hazards and Assess Risks: For each task, identify the potential hazards that could arise. Consider physical, chemical, biological, ergonomic, and psychosocial hazards. Consult workers, supervisors, and safety experts to ensure a comprehensive identification process. Evaluate the risks associated with each identified hazard. Determine the likelihood and severity of the risks to prioritize control measures.
c. Implement Controls: Develop control measures to eliminate or minimize the identified hazards. This can include engineering controls, administrative controls, and personal protective equipment (PPE). Select the most effective control measures for each hazard. Consider industry best practices and regulatory requirements in implementing controls.
d. Seek Professional Review: It is recommended to have a safety professional review the JHA you have created. They can provide valuable insights, ensure compliance with regulations, and offer recommendations to further enhance safety measures. Additionally, you can use tools like ChatGPT or similar AI tools to create a preliminary draft list of Task-Risk-Controls. However, the final review and recommendations should always be conducted by a qualified safety professional.
Remember, developing an effective JHA requires collaboration, input, and expertise from various stakeholders. By following these steps and seeking professional guidance, you can create a comprehensive JHA that enhances safety and minimizes the risks associated with the job or task at hand.
Pre-Task Plans (Pre Shift Plans) play a crucial role in enhancing construction safety and efficiency. By analyzing potential hazards, implementing control measures, and promoting a proactive safety culture, these plans significantly reduce the risk of accidents and injuries. Through compliance with regulations and the adoption of best practices, construction companies can prioritize the well-being of their workers and contribute to the overall success of their projects.
Safety Best Practices
Stefano Braganti
Labor drift, rework and schedule slips thrive when you can't see head-count live. Learn how smart turnstiles & dashboards give GCs real-time visibility.
Safety Best Practices
Stefano Braganti
Stop-Work Orders crush margins. Digital safety dashboards catch risks early, prevent claims, and protect your 3% fee.
Safety Best Practices
Stefano Braganti
NYC DOB formalizes digital record-keeping: what the bulletin says, why it matters, and how SafetyClerk helped make it happen.
together
SafetyClerk is the construction management platform that makes safety compliance, and risk management of your job site simple and visible in one click.
Stay on
the loop!
ConstructionClerk - 2025 - All rights reserved
ConstructionClerk - 2025 - All rights reserved